For the past few months, my project partner, Seila De Leon, and I have been given the challenge of creating a soil-drying field device for the Ucross Quick Carbon project. As Seila explained in her first blog post, we were initially given this assignment as a final project last fall semester. We then chose to continue working with Ucross as research interns during the spring semester, and now as Western Research Fellows. The soil-drying device is necessary because Ucross uses light spectrometers to measure carbon content in soil based on the correlation between soil color and the amount of carbon present. Moisture in soil causes it to be darker in color, which interferes with the accuracy of the light spectrometer carbon readings.
Throughout the summer, we have done a lot to improve our device, in terms of both efficiency as well as transportability in the field. When we traveled to Ten Sleep, Wyoming for the WRF Retreat, Seila and I were happy to bring our most recent prototype with us. This device can effectively dry a 5 gram soil sample with a 12% moisture content down to a 2% moisture content in two minutes. To produce these results, we utilized heat conduction with two 5 cm x 10 cm heating pads that reach 200 degrees Celsius and heat convection with a small 3 cm x 3 cm x 0.7 cm fan that runs for 3 seconds out of every 10 seconds.
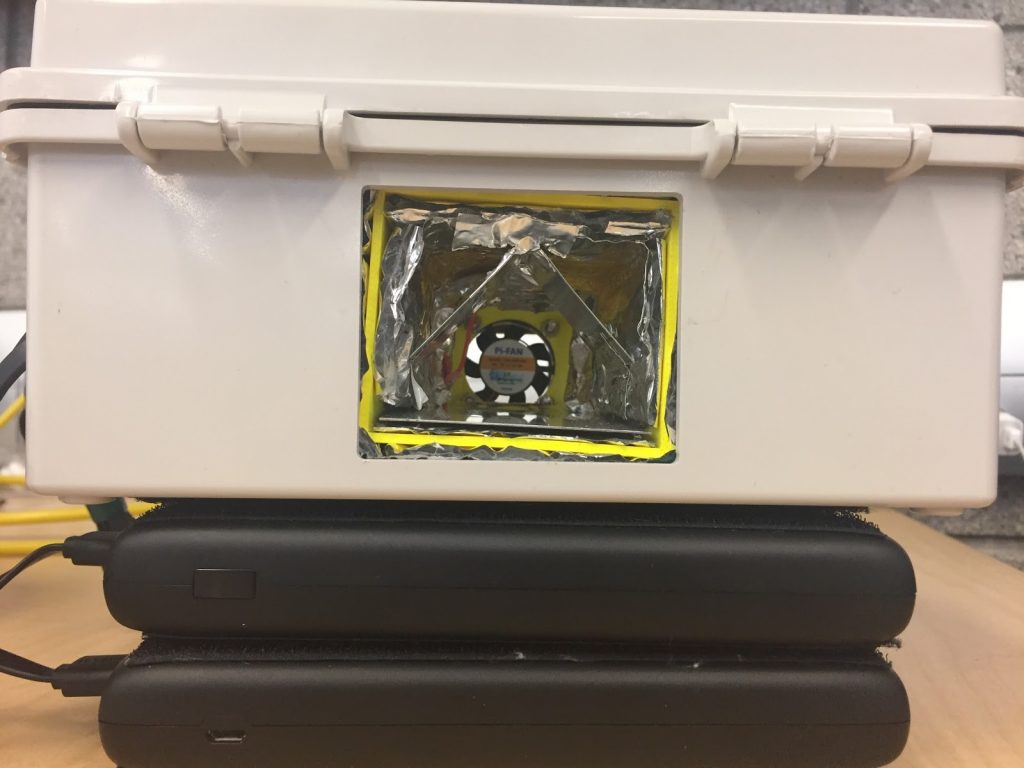
Above is a view of the internal heating chamber and fan in the prototype taken to Wyoming.
Having reached this point in our work, I was excited to get my first taste of field work in hopes that it would give some inspiration for more changes that could improve the dryer. Our field experience in Ten Sleep did not disappoint in allowing us to look at the dryer from a new perspective, outside of Yale’s Center for Engineering, Innovation, and Design work space. The trip provided us with vital insight about what we should be improving and focusing on for the remainder of the summer.
One of our biggest hurdles to overcome throughout the summer has been figuring out how to power our device without access to an electrical outlet in the field. The prototype that we took to Ten Sleep is powered by four 5V battery packs in series, giving us a total of 20V of power. Although our design has become much more compact throughout our work, we have doubled the number of battery packs used, which has significantly increased the weight of the dryer. When Seila and I went out in the field with all of the equipment that a Quick Carbon field tech team would carry, we saw that our dryer is still larger and heavier than is ideal.
So, since returning from Wyoming, we have focused on making our final soil dryer prototype both smaller and lighter than the one we took with us in the field. Using all of the same components as this most recent dryer, we knew we would be able to decrease the size of the dryer box by about a third in terms of volume. However, I have focused a large portion of my time these last few weeks on minimizing the size of all electrical components. Hopefully this will allow us to fit everything into a box that is about half of the size of the prototype taken to Wyoming (this one is already about half as big as our first prototype that was turned in as a final project).
Additionally, I have had a lot of fun working with a DeWALT drill and battery to try to power the heating pads off of one 20V, 5Ah drill battery instead of the four 5V battery packs in series. The fan and LCD that displays the temperature of the heating pads in the dryer will be powered off of three rechargeable 9V batteries in parallel. This change will greatly reduce the volume and weight that the power supply contributes to the dryer.
To set up this power arrangement, I had to disassemble the drill and take just the charging piece that sits at the bottom of the handle. I then sawed off the bottom of the drill handle. This piece will be permanently mounted on the bottom of this summer’s final dryer prototype. The drill battery will then slide into place, as it would on a normal drill.
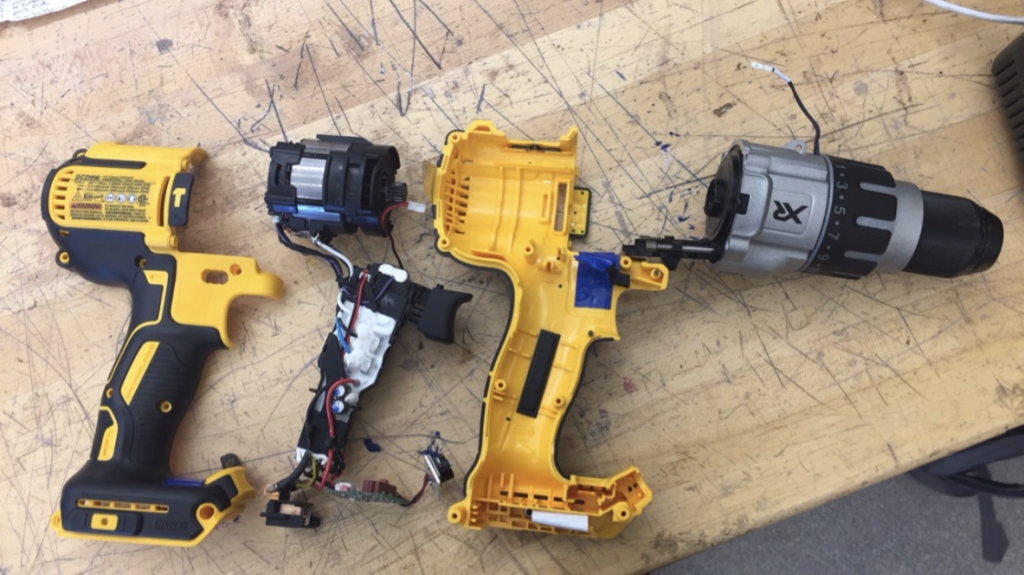
Here is the fully disassembled drill. The only part we will use to power the dryer is that below the handle that contains the electrical piece that connects to the battery.
This change is good for minimizing weight and size of the dryer, as well as creating a more uniform Quick Carbon kit. The DeWALT drill batteries used for the dryer are the exact same rechargeable batteries the field techs use to power the drills in the soil extractors. Hopefully our final prototype, which is scheduled to be completed next week, will be a useful and manageable piece of equipment for Quick Carbon researchers out in the field.